Ampacet Denestur™, Eases Single-Unit Separation To Reduce Downtime And Material Costs
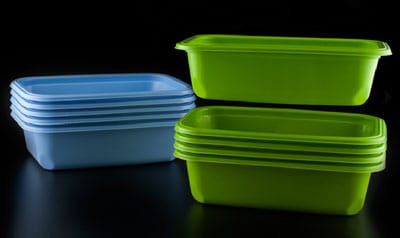
DeNestur ™, a new anti-static de-nesting additive masterbatch from Ampacet, simplifies injection and thermoforming; features cost-saving efficiencies in high speed automated packaging of single-serve food and beverage products; and creates a waste-reducing, consumer-friendly, brand-enhancing cup dispensing experience at convenience store and food service locations.
Ampacet DeNestur™, a new de-nesting additive masterbatch, provides processing benefits for thermoformers and injection molders, faster line speeds and less waste for packagers and processors, and quick and easy single-serve food and beverage tray and cup separation for retail operators and consumers.
Ampacet DeNestur™ imparts an easy-glide, anti-static, no-stick characteristic for improving molder/thermoformer production output efficiencies and material cost savings by eliminating build-up from the mold and machine surfaces. As the technology is built into Ampacet DeNestur™, no secondary top-coat application is necessary.
The result is friction reduction of up to 70% for PET, PE and PP; from 25% to 50% lower force required for mold release and de-nesting; reduction in scratch depth of up to 50%, and improvement of 10-25% in packing density.
In packaging and processing operations, the high-performance de-nesting additive helps to eliminate packaging machinery jamming, equipment damage, and material waste, resulting in higher line speed potential, better line speed consistency and less downtime.
Use of Ampacet DeNestur™ also helps to improve the brand experience at convenience store and food service outlets for consumers by providing easier container separation at point of service, and cuts material and labor costs for retail operators by eliminating container waste and in-store mess.
Ampacet DeNestur™ additive masterbatch formulations can be used in conjunction with a white and black masterbatch and custom color formulations. It can also be used as a stand-alone additive for use with polypropylene (product 40604), polyethylene (product 10090) and PET (product 703853) resins. Ampacet DeNestur™ is FDA compliant, with no effect on color, clarity or resin properties.